Gauge Fillet Weld Essentials: Best Practices and Common Mistakes
Gauge Fillet Weld Essentials: Best Practices and Common Mistakes
Blog Article
Fillet Weld Layout Methods: Maximizing Joint Performance and Aesthetics for Structural Honesty
In the realm of architectural engineering and construction, the value of fillet weld layout methods can not be overemphasized. By thoroughly thinking about elements such as weld profile optimization, material selection, joint prep work methods, welding process performance, and aesthetic improvement producers, methods and engineers can attain a harmonious equilibrium in between capability and look in their welded structures.
Weld Account Optimization
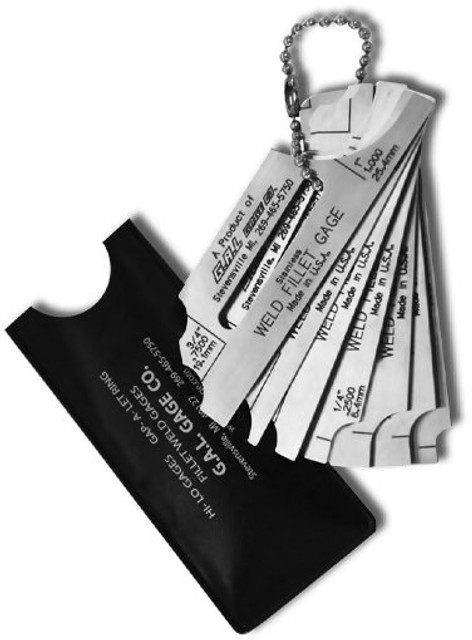

Achieving an ideal weld profile includes a meticulous consideration of aspects such as material thickness, joint configuration, welding placement, and preferred welding rate. In addition, the selection of appropriate welding specifications, such as voltage, existing, and take a trip rate, is fundamental in managing the form and measurements of the fillet weld. Making use of advanced welding methods, such as pulse welding or robot welding, can better fine-tune the weld profile to satisfy details layout needs and high quality standards.
Essentially, weld profile optimization is a basic facet of fillet weld design that directly affects the total efficiency and dependability of welded joints in architectural applications.
Product Option Factors To Consider
When considering material option for fillet weld layout, the compatibility of the base steels is a critical factor affecting the architectural honesty of the joint. It is vital to choose products that not just bonded with each other efficiently however also have comparable mechanical residential properties to make sure the tons is uniformly distributed between the weld and the base metals. Welding materials with vastly various buildings can bring about concerns such as stress focus, early joint failing, or splitting.
Furthermore, the environment in which the bonded framework will run must be considered when selecting products. Elements like corrosion resistance, temperature level changes, and exposure to chemicals can all affect the long life and efficiency of the weld joint. By choosing products that appropriate for the intended application and atmosphere, the total longevity and integrity of the bonded joint can be significantly enhanced.
Consequently, thorough factor to consider of material compatibility and ecological aspects is paramount in ensuring the weld joint's toughness, toughness, and overall architectural integrity.
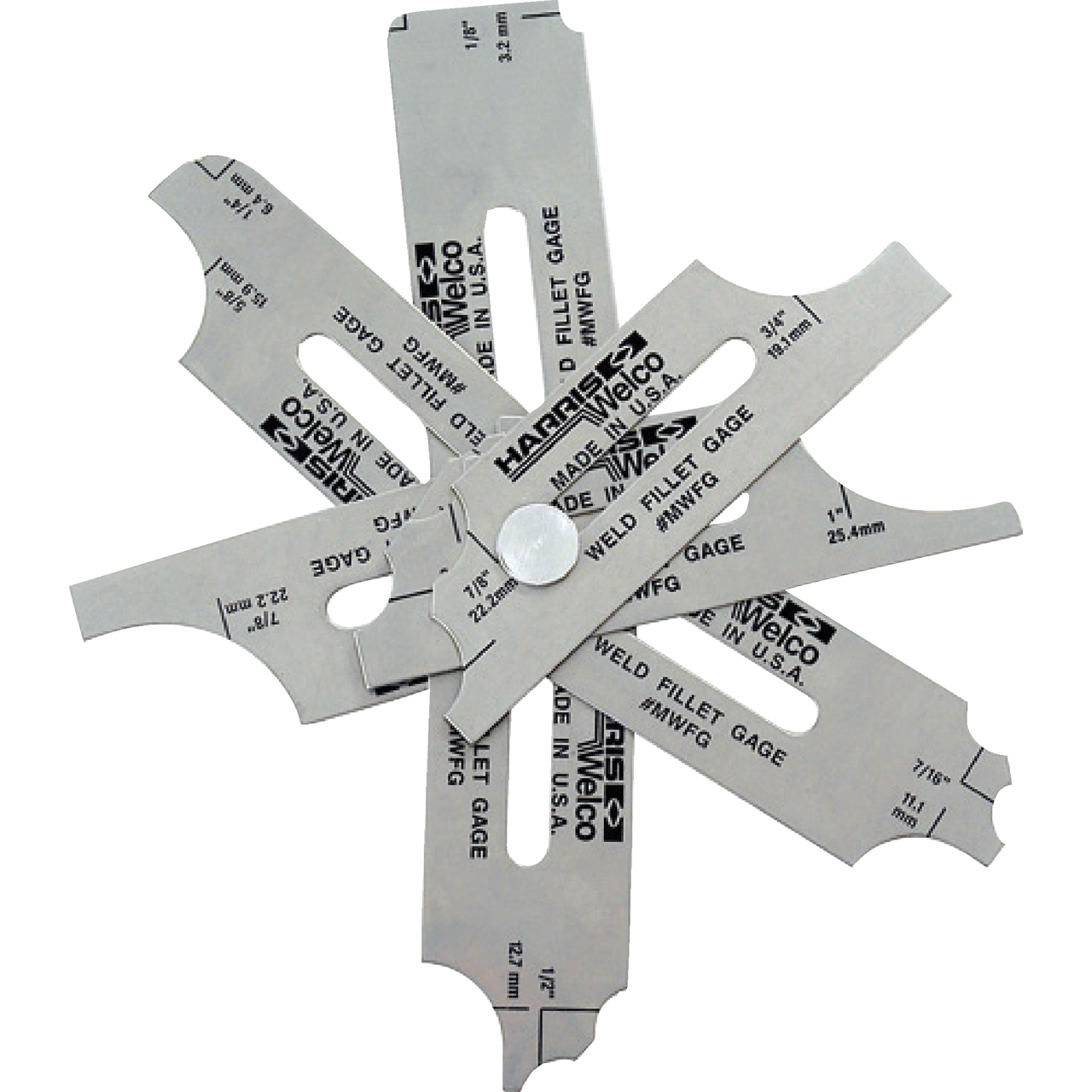
Joint Preparation Strategies
Taking into consideration the vital duty material choice plays in making certain the architectural integrity of fillet weld joints, it is vital to apply exact joint prep work strategies that enhance the link in between the base steels. Joint prep work is a crucial step that directly influences the high quality and toughness of the weld. One basic strategy is the cleansing of base metals to remove any kind of contaminants like rust, oil, or paint that might compromise the weld's integrity. This can be attained via methods such as grinding, wire brushing, or chemical cleaning.
Furthermore, proper fit-up of the joint is vital to guarantee consistent circulation of the welding product their explanation and stop problems like incomplete penetration or excessive buildup. Beveling the sides of the base metals can develop a groove that enables much deeper weld infiltration and a more powerful bond. Furthermore, tack welding the components in area prior to the last weld aids preserve alignment and lessens distortion during the welding process. By meticulously adhering to these joint prep work techniques, welders can boost the general performance and appearances of fillet weld joints while making certain architectural strength.
Welding Process Performance
Effective welding procedures are vital for accomplishing optimum efficiency and quality in fillet weld manufacture. One key element of enhancing welding procedure efficiency is choosing the ideal welding technique. Aspects such as material type, joint layout, and welding setting need to be thoroughly taken into consideration to identify one of the most suitable approach. Procedures like gas steel arc welding (GMAW) and flux-cored arc welding (FCAW) are commonly utilized for fillet welds due to their adaptability and speed.
Moreover, guaranteeing appropriate devices configuration and upkeep is crucial Going Here for reliable welding. Routine calibration of welding makers, assessment of consumables, and maintenance of welding torches can avoid downtime and rework, inevitably conserving time and resources. Furthermore, using knowledgeable welders with expertise in the specific welding procedure being used can substantially affect effectiveness. Well-trained welders are much more proficient at adjusting parameters, troubleshooting problems, and preserving constant weld quality.
Visual Enhancement Methods
To maximize the quality of fillet weld construction, executing aesthetic improvement approaches can play a critical function in guaranteeing accuracy and accuracy during the welding procedure. Visual improvement techniques encompass different techniques intended at improving the look and high quality of fillet welds. One common strategy is using back removing systems to eliminate oxidation on the behind of the weld, resulting in a cleaner, a lot more aesthetically pleasing coating. Furthermore, using proper illumination setups in the welding area can improve exposure, enabling welders to monitor the weld swimming pool and guarantee consistent grain formation. Aesthetic aids such as weld size determines and magnifying lenses can assist in assessing weld accounts and measurements accurately. The use of contrasting marking materials or momentary adding can assist in straightening and positioning the work surfaces exactly prior to welding. By integrating these visual enhancement methods into the welding procedure, welders can achieve not just structurally sound fillet welds however also visually appealing results that meet industry requirements.

Verdict
Finally, maximizing fillet weld design entails careful factor to consider of weld profile, material selection, joint prep work, welding process effectiveness, and visual enhancement approaches. By carrying out these strategies, architectural honesty can be improved while likewise attaining aesthetic charm. It is very important to prioritize both performance and aesthetic appeals in fillet weld layout to ensure the overall high quality and longevity of the joint.
By thoroughly taking into consideration elements such as weld profile optimization, product choice, joint prep work strategies, welding process efficiency, and aesthetic improvement designers, producers and approaches can attain a harmonious balance in between functionality and appearance in their welded structures.In the realm of fillet weld layout, maximizing the weld account plays a vital role in guaranteeing architectural stability and efficiency. The weld profile, which includes the dimension and form of Look At This the weld cross-section, straight affects the circulation of tension and load-bearing capability within the joint. It is essential to pick products that not only bonded together efficiently but also have comparable mechanical buildings to make certain the tons is evenly distributed between the weld and the base metals - Gauge Fillet Weld.In conclusion, optimizing fillet weld layout entails cautious consideration of weld profile, product choice, joint preparation, welding procedure efficiency, and visual improvement approaches
Report this page